Hydrogen production is a key technology for the energy transition and industrial processes, particularly in the chemical, energy and automotive industries. High-purity water is an essential prerequisite for many hydrogen production processes, such as electrolysis, which is one of the most efficient and sustainable methods. The quality of the water used has a decisive influence on the efficiency, service life and operational safety of the systems. Ultrapure water and fully demineralized water (demineralized water) meet the demanding requirements for these processes.
Table of contents
Importance of water quality in hydrogen production
During hydrogen production, particularly through electrolysis, water is broken down into hydrogen (H₂) and oxygen (O₂). The purity of the water used is crucial, as impurities can cause corrosion, fouling or membrane damage in the electrolysis cells.
Water quality requirements
Ultrapure water for electrolysis:
- Leitfähigkeit: Extrem niedrige Werte (< 0,1 µS/cm), um elektrische Kurzschlüsse und Ablagerungen in den Elektroden oder Membranen zu verhindern.
- Organic compounds: Virtually no organic impurities, as these can interfere with the efficiency of electrolysis.
- Particle-free: Suspended particles and colloids must be completely removed to prevent mechanical damage to the systems.
- Ion concentration: No dissolved ions such as sodium, chloride or sulphate, as these can lead to corrosion.
Demineralized water for technical processes:
Demineralized water (DI water) is less pure than ultrapure water, but meets the requirements for less critical hydrogen production processes or supporting systems such as steam generators.- Conductivity: Below 20 µS/cm.
- Hardness-free: No calcium or magnesium ions to prevent deposits.
Water treatment for hydrogen production: Insights and technologies
Water treatment for hydrogen production requires highly developed technologies in order to meet the requirements for the quality of ultrapure water and demineralized water. The choice of process depends largely on the origin of the water to be treated. While well water is often contaminated with a high content of hardness constituents, iron or manganese, municipal water usually has a standardized basic quality, but often contains chlorine and organic compounds that need to be removed. Both water sources require customized treatment processes to ensure the efficiency of hydrogen production.
1. pretreatment
Pre-treatment is crucial to protect the subsequent treatment stages from contamination and to ensure consistent water quality. It is individually adapted to the specific contamination of the raw water.
Origin of the water and specific requirements
- Well water:
- Frequently increased concentrations of iron, manganese and hardness constituents.
- Possible turbidity due to colloidal particles or microbiological contamination.
- Requires additional stages such as iron removal, manganese removal or precipitation and flocculation.
- City water:
- Chlorine and disinfection by-products must be removed as they can damage membranes and ion exchange resins.
- Organic compounds and odorous substances pose a challenge.
- Activated carbon filters play a key role.
Typical pre-treatment methods
- Multi-layer filter:
Removes suspended solids, particles and coarse impurities. The layering of quartz sand, anthracite and gravel efficiently retains particles of different sizes. - Activated carbon filters:
Adsorb chlorine, organic compounds and odorous substances. Activated carbon protects downstream membranes from chemical damage. - Precipitation and flocculation:
Colloidal particles, phosphates or dissolved metals are converted into solid particles by chemical reactions, which are then removed by sedimentation or filtration.
Photo: Our double filtration system with sand and activated carbon
2. membrane process
Membrane processes are the backbone of water treatment for hydrogen production, especially when ultrapure water is required.
Reverse osmosis (RO):
- Function:
In reverse osmosis systems, the raw water is pressed under high pressure through semi-permeable membranes that almost completely retain dissolved salts, organic substances and micropollutants. - Performance:
Removes up to 99 % of dissolved salts and pollutants. Particularly suitable for removing heavy metals, nitrates and organic residues. - Application:
First main stage of demineralization, especially for water with high conductivity or salt content.
Electrodeionization (EDI):
- Function:
A combination of ion exchange and electrochemistry that continuously produces ultrapure water. The resins are regenerated by electric fields without the need for chemical regeneration agents. - Leistungsfähigkeit:
Erreicht Leitfähigkeitswerte von < 0,1 µS/cm. - Application:
Ideal supplement to reverse osmosis to remove the last traces of ions and meet the highest purity requirements.
Photo: Our ALMA OSMO reverse osmosis system for producing demineralized water
3. ion exchanger
Ion exchangers are indispensable for the selective removal of specific ions from water. They can be used flexibly and are economical, especially with fluctuating raw water qualities.
- Anion exchangers:
Remove chloride, nitrate and sulphate ions that can cause corrosion or fouling. - Cation exchanger:
Removes hardness formers such as calcium and magnesium, which lead to deposits. - Mixed bed resins:
Combine anion and cation exchangers and provide particularly pure water. Often used in combination with EDI.
Advantages of ion exchangers:
- High selectivity for specific ions.
- Regenerable resins reduce chemical consumption.
- Suitable for the production of demineralized water and as a polishing step for ultrapure water.
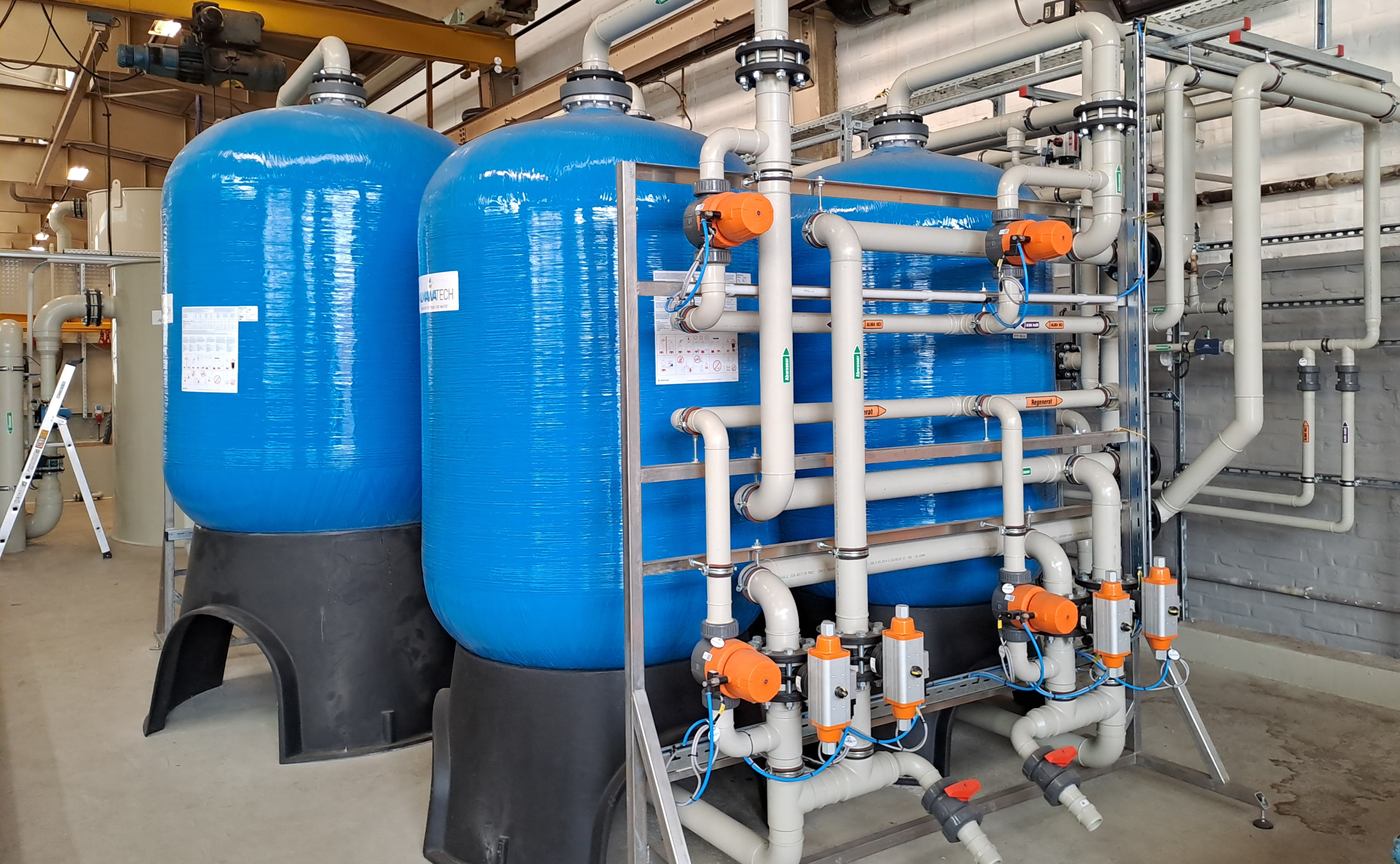
Photo: Our ALMA ION ion exchanger system with upstream ALMA FIL multi-layer filter
Key technological processes in practice
The specific combination of technologies depends on the raw water quality and the final requirements. Typical examples are
Combination of reverse osmosis and EDI:
- Application: Production of ultrapure water for proton exchange membrane electrolyzers (PEMEL).
- Advantage: Virtually chemical-free operation and consistent quality.
Ion exchanger for demineralized water:
- Application: Production of deionized water for alkaline electrolysers.
- Advantage: High flexibility and easy integration into existing systems.

Photo: Our ultrapure water system with softening, reverse osmosis and EDI, for small water flows
Areas of application for hydrogen production
Industrial hydrogen production requires high-purity water for a wide range of applications:
energy industry:
- Electrolysis-based hydrogen production for fuel cells and power-to-gas applications.
Chemical industry:
- Production of hydrogen as a starting material for ammonia and methanol production.
Automotive industry:
- Hydrogen for fuel cell vehicles (FCEV).
Metallurgy:
- Use of hydrogen as a reducing agent in steel production.
pharmaceutical and electronics industries:
- Ultrapure water for sensitive production processes with the highest requirements.
Conclusion
Hydrogen production is closely linked to the availability of high-purity water. The production of ultrapure and demineralized water requires the targeted use of modern water treatment technologies such as reverse osmosis, EDI and ion exchangers. Ensuring water quality is not only crucial for the efficiency and service life of the systems, but also for the sustainable use of resources. Innovative plant concepts and modular systems enable the requirements of the hydrogen industry to be met reliably and economically.
For further information on our products, please feel free to contact us at any time!